르노코리아자동차는 지난 4월 한 달간, XM3 5,588대(수출명 르노 아르카나, E-TECH 하이브리드 포함), QM6(수출명 르노 꼴레오스) 2,177대, 총 7,779대를 선적했다. 3월에는 XM3 1만 939대, QM6는 2,037대, 총 1만 2,985대를 배어 실었던 르노코리아였다.
XM3의 선적량이 눈에 띄게 줄었다. 대체 무슨 일이 있었던 걸까? 르노코리아자동차는 4월 실적을 발표하면서 ‘선적 스케줄에 따른 일시적 영향’이라는 설명을 달았다. 무엇이 한 달 사이 XM3 5,351대의 수출길을 막아선 걸까?
최근 르노코리아자동차는 미디어 관계자들이 부산 공장 생산라인 및 수출차량 선적 현장을 견학할 수 있는 프로그램을 마련했다. 보통 공장 견학은 특별한 이슈가 있을 때 추진된다. 새로운 라인이 가동되거나 신기술이 도입됐을 때, 취재진 견학 프로그램을 가동한다. 최근에 그런 이슈는 없었다.
핵심은 수출차량 선적 현장이었다. 여기에도 의외의 요소가 있었다. 대개 이런 주제라면 부두에서 자동차 전용선에 차를 싣는 현장이 더 어울린다. 수 천대의 차가 끝도 없이 전용선을 오르는 모습은 압도적이다.
르노코리아가 취재진에게 보여준 곳은 부두가 아니라, 부산공장의 한 켠에 마련된 수출 차량 컨테이너 선적 현장이었다. 여기서 또 궁금증이 터진다. 자동차를 컨테이너에 넣어 보낸다고?
정말로 현장에는 대형 컨테이너가 두 대가 나란히 대기하고 있었다. 그리고 컨테이너의 뒤편으로는 공장에서 출하된 XM3 3대가 줄을 지어 서 있었다.
컨테이너로 올라가는 철제 경사로가 만들어져 있고, 그 길을 따라 XM3가 한 대씩 들어갔다. 후진으로 첫 번째 XM3가 올라간 뒤, 차량이 흔들리지 않게 단단하게 고정하는 작업이 이뤄졌다.
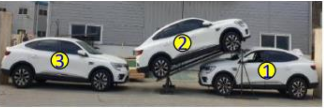
두 번째 차가 올라갈 차례다. 작업자들이 뭔가를 준비하며 분주히 움직였다. 차가 컨테이너 안에서 경사면으로 포개질 수 있는 받침대를 설치하고 있었다. 잠시 뒤 두 번째 XM3가 컨테이너로 들어가더니 첫 번째 차를 타고 오르듯 경사면에 고정됐다.
두 번째 차량의 고정작업이 끝나자 세 번째 XM3가 컨테이너로 들어갔고, 고정 작업 후 그제서야 컨테이너의 문이 닫혔다.
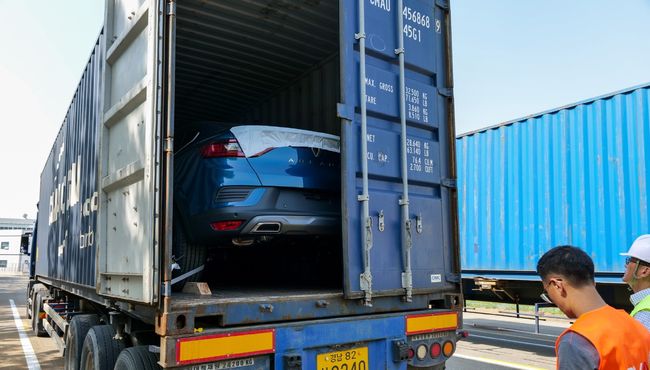
이제야 모든 의문이 풀렸다. XM3의 수출실적이 한 달 사이 5,000여대가 빠진 이유는 자동차 전용선을 구하지 못한 때문이었고, 르노코리아자동차가 백방으로 뛴 끝에 컨테이너 수출 방식을 고안해 수출길을 다시 열었던 거다. 그렇게 애쓴 현장을 미디어 관계자들에게 보여주고 싶었던 게다.
자동차를 컨테이너에 실어 보내는 건 간단한 작업이 아니다. 우선 해당 관청의 양해가 있어야 한다. 관련 부처만 해도 산업통상자원부, 해양수산부, 부산광역시가 첩첩이 있다. 르노코리아에서 대관업무를 하는 임원이 이리 뛰고 저리 뛰었다. 다행히 모든 관청이 적극적으로 협조했다. 무역협회도 발벗고 나섰다. 이제 행정적인 문제는 없어졌다.
남은 건 차를 컨테이너에 효율적으로 적입하는 일이다. XM3가 소형이기는 하지만 일반적으로 실어서는 3대를 넣을 수가 없다. 그렇다고 두 대만 실어 보내기에는 빈 공간이 너무 남는다. 그래서 고안해 낸 게 포개기 선적이다. 차끼리 안전한 거리를 유지할 수 있는 구조물도 만들어졌다. 차를 싣고 내리는 작업은 대행업체가 맡아 하기로 했다.
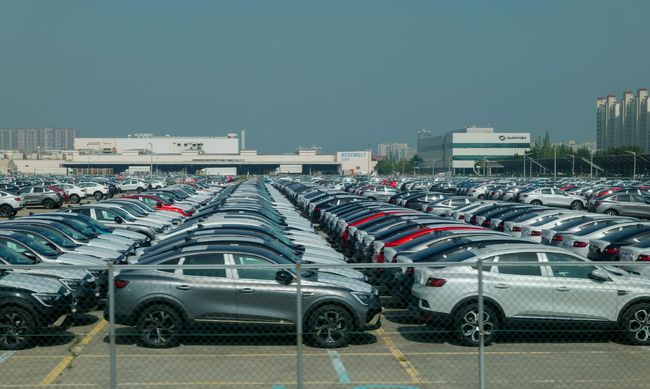
기대하지 않은 효과도 생겼다.
선적 비용이 자동차 전용선 보다 10%나 낮았다. 컨테이너로 차를 보내기 때문에 기항이 뜸한 전용선 보다 수출선을 구하기도 쉬웠다. 또 완성된 차를 공장으로부터 10km 떨어진 부두로 보내는 게 아니라 공장에서 컨테이너에 바로 싣기 때문에 물류비용도 절감할 수 있다.
컨테이너 수출 현장을 소개한 르노코리아 이선희 담당은 “2010년부터 2020년까지 6,000대 기준 1년 용선료는 2만 달러 수준이었다. 그러던 것이 코로나19가 창궐한 시기에 맞춰 급등하기 시작해 2022년에는 8만 달러까지 치솟았다”고 말했다.
치솟은 용선료보다 더 큰 문제도 있었다. 최근 중국의 자동차 수출이 크게 늘면서 자동차 전용선을 싹쓸이하다시피 했다. 르노코리아자동차가 컨테이너 수출길이라도 찾아내야 하는 배경이었다. 전용선사를 보유하지 않고 있는 르노코리아로서는 궁여지책이라도 꺼내야 할 판이었다.
4월부터 새 방법을 찾아낸 르노코리아는 이제 수출물량의 10%를 컨테이너 선적으로 소화하고 있다. 전용선이 없어 수출을 못하는 답답한 환경은 르노코리아와 정부의 관계부처가 힘을 모아 돌파구를 찾았고, 비로소 한숨을 돌릴 수 있었다.
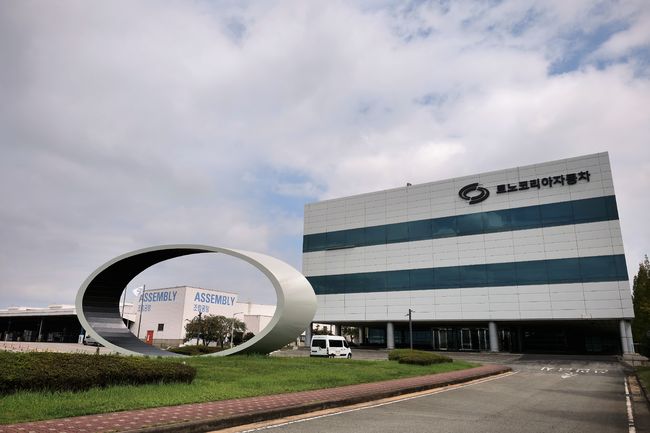
르노코리아자동차의 부산공장은 연간 최대 30만대까지 생산할 수 있는 설비를 갖추고 있다. SM3와 SM5가 잘 팔리던 2010년에는 연간 27만 5,000대를 생산한 적도 있다.
큰 위기도 맞았다. 2011년과 2012년 두 해 동안 5,000억원이 넘는 적자를 기록할 때가 많이 힘들었다. 이 위기는 리바이벌 플랜의 성공적인 시행과 2014년 하반기 닛산 로그 물량 생산을 맡으면서 정상화 시켰다. SM6가 인기를 끌고 닛산 로그 수출물량까지 생산하던 2017년에는 26만 4,000대를 뽑아냈다.
닛산 물량이 빠진 2020년에는 11만 2,000대까지 떨어졌다가 XM3의 수출이 활기를 띠면서 2022년에는 16만 8,000대까지 회복이 됐다.
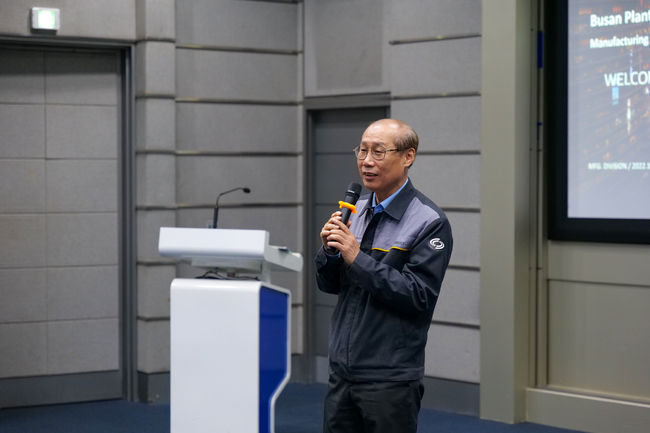
부산공장 소개를 맡은 제조본부 이해진 본부장은 “르노코리아 부산공장은 르노그룹 내 세계 21개 공장 중 품질 평가에서 항상 1, 2위를 다투고 있다”고 자랑했다. 이 본부장은 “품질 제일주의의 삼성 DNA가 아직 우리 공장 직원들 사이에 흐르고 있다”는 말로 품질에 대한 자신감을 에둘러 표현했다.
르노의 삼성 공장이 고품질을 유지할 수 있는 비결로는 ‘다양한 차종의 혼류 생산도 거뜬히 해 내는 직원들의 높은 숙련도’를 꼽았다. 부산공장에서는 완성차 뿐만 아니라 엔진과 차체도 혼류생산을 해낸다. 작업자들이 헷갈리지 않게 조립 부품을 자동으로 공급하는 시스템(AGV, Auto Guided Vehicle)이 갖춰져 있기 때문에 혼류 생산으로 인한 혼선은 없다.
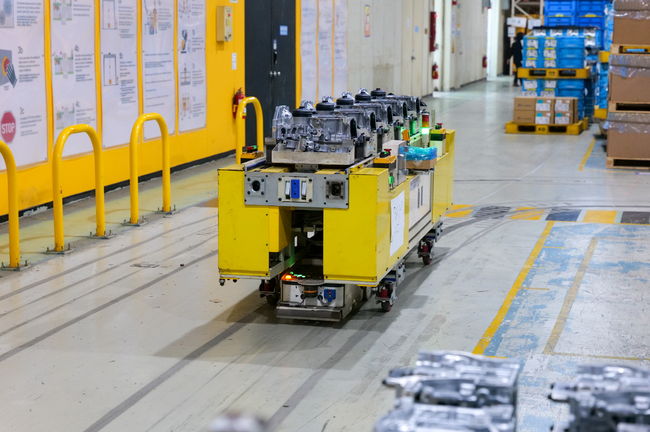
부산공장은 최신 자동화 시설 아래 1개의 조립 라인에서 4가지 플랫폼의 8개 모델까지 혼류생산할 수 있다. 파워트레인도 가솔린, 디젤, 전기차, 하이브리드를 가리지 않는다. 실제로 2016~2019년 7개 차종(SM3, SM5, SM6, SM7, QM6, 닛산 로그, SM3 ZE 전기차)을 동시 생산했으며, 현재는 3개 차종(XM3, SM6, QM6)을 1개의 조립 라인에서 뽑아내고 있다.
수출 효자는 역시 XM3다.
XM3(수출명 르노 아르카나)는 2020년 7월 칠레 수출을 시작으로 2020년 909대, 2021년 5만 6,719대, 2022년 9만 9,166대 등 지난해까지 누적 수출 실적 15만 6,794대를 해냈다.
XM3가 환하게 빛나기 시작한 건 2021년 6월, 유럽 시장 판매를 시작하면서부터다. 유럽 시장에 하이브리드 모델을 국내보다 먼저 선보이며 생산량도 급격히 늘었다. XM3 하이브리드 모델의 수출은 2021년 3만 701대에서 2022년 5만 8,778대로 가파른 증가세를 보였다.
르노코리아자동차는 2022년 한 해 동안 유럽 지역에 XM3 9만 3,251대, QM6(수출명 르노 꼴레오스) 5,088대 , 총 9만 8,861대를 수출했다. 두 차종은 같은 기간 전체 수출 물량 11만 7,020대의 84.5%를 차지했다. 창사 이래 유럽 지역 최대 수출 실적을 달성했다.
공장 한 켠에 배터리 조립라인이 자리잡고 있는 모습도 인상적이었다. XM3 하이브리드에 들어갈 배터리를 공장에서 직접 조립하고 있었다. 배터리 조립라인은 혹시 모를 화재에 대비하기 위해 별도의 파이어월로 사방이 둘러싸여 있었다. 화재시에는 파이어월로 조립라인이 밀폐된 상태에서 천장에서 고압의 물이 뿌려진다.
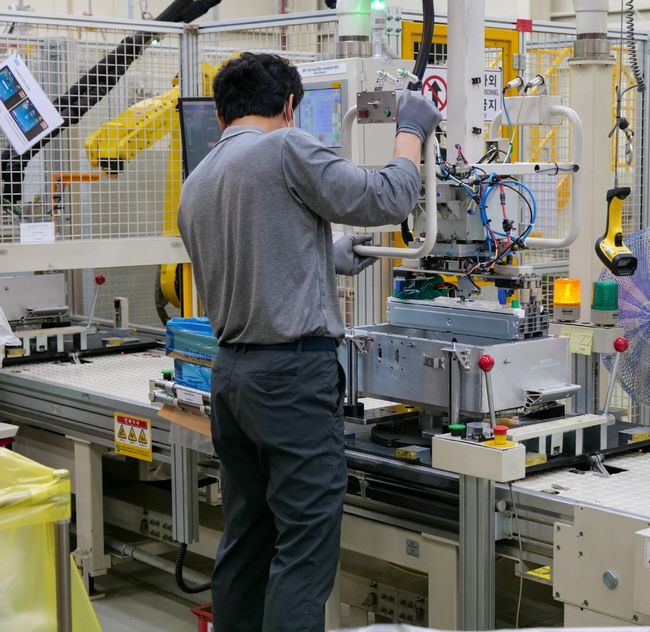
물론 이 곳에서 전기차 배터리까지 조립되는 건 아니다. 본격적인 전동화 차량 생산을 위해, 별도의 공장부지를 마련해 놓았다.
부산공장 제조본부 이해진 본부장은 “르노코리아는 한국에서의 열악한 제조환경에도 불구하고 품질 높은 완성차를 모범적으로 생산하고 있다”고 말했다. /100c@osen.co.kr