자동차의 패러다임이 전기차로 옮겨간다고 해서 차를 만드는 공장이 반도체 공장처럼 적막해 질 수는 없다. 초대형 프레스는 기괴한 리듬으로 심장을 흔들어야 하고, 프로그래밍 된 로봇팔은 사방으로 용접 불꽃을 튀겨야 하며, 조립라인에 선 노동자들은 끊임없이 반복 작업을 수행해야 한다.
여느 자동차 공장과 별반 다를 게 없어 보이는 이 곳 공장에서 내연기관차가 아닌 전기차가 생산 돼 나온다. 결과물만 보는 외부인의 시선에선 판단의 오류가 발생하기 딱 좋은 조건이다. “내연기관이 조립되던 공정을 뚝딱 바꾸면 전기차가 생산 되는 것 아닌가?”
폭스바겐그룹의 대표적인 전기차가 생산되는 독일의 하노버 공장과 츠비카우 공장에 가서 그 곳 사람들의 말을 듣기 전까지는 기자도 그런 오류에 빠져 있었다.
지난 5월 말, 독일 동부 작센주에 있는 츠비카우 공장을 한국 기자단이 찾았다. 1990년, 축구장 252개 면적인 180만 제곱미터의 부지에 설립돼 2019년까지 폭스바겐 골프와 골프 변종 모델을 생산하던 내연기관 생산라인의 본산이다. 전동화 이후인 2021년에는 연간 17만 9,179대의 완성차와 람보르기니 같은 고급모델의 차체 1만 1,383대가 생산됐다. 상주직원 9,500명이 생산하는 물량치고는 적은 수치다.
그럴 만한 이유가 있었다. 이 공장은 폭스바겐그룹이 12억 유로(약 1조 6,000억 원)를 투자해 내연기관 공장에서 100% 전기차 생산공장으로 전환한 그룹 최초의 현장이기 때문이다. 건물 외관은 종전 공장과 다를 게 없지만 내부 공정은 전동화 생산라인으로 탈바꿈돼 있었다.
기존 공장 건물로 허물고 새로 지은 게 아니라 건물은 두고 내부 라인만 손질을 했다. 왜 일까? 폭스바겐그룹 관계자는 ‘지속가능성의 일환’이라고 설명했다. 싹 허물고 새로 짓는 게 효율적일 수 있지만 그러지 않았다고 했다.
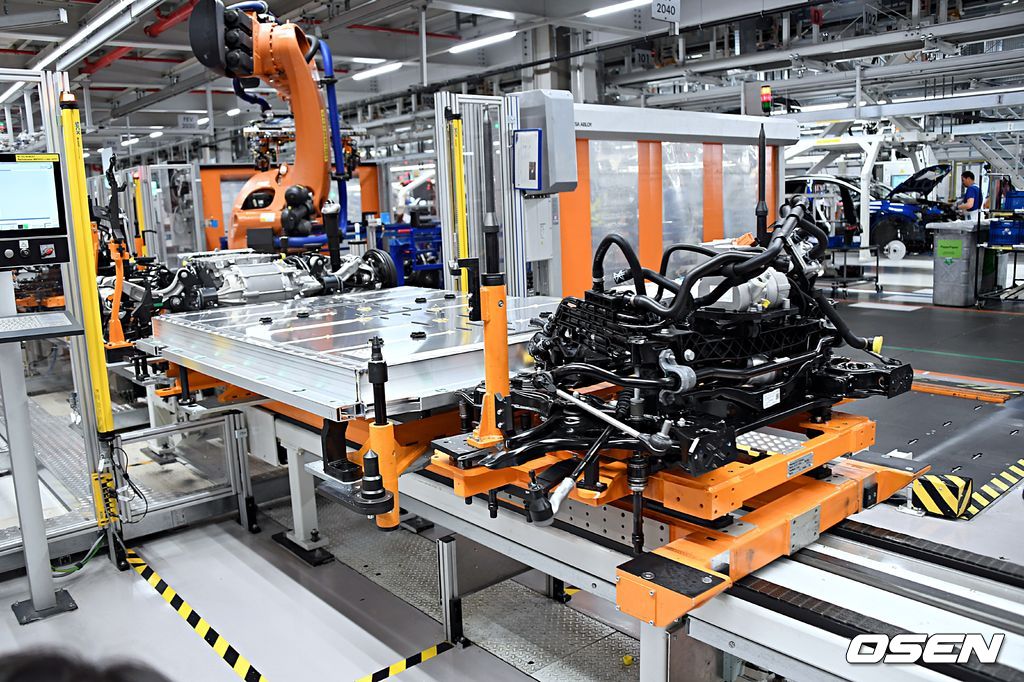
그들이 따로 시간을 내 들려 준 이야기를 듣고나니 왜 하필 ‘지속가능성’인지 이해가 간다. 그들은 ‘파괴와 재창조’가 아닌, 대전환(트랜스포메이션, Transformation)을 선택했기 때문이다.
공장을 뜯어고치는 일은 사실 낮은 수준의 ‘전환’이었다. 진짜 핵심은 ‘사람’이었다.
그들은 인력을 쓰는 방식에도 ‘지속가능성’을 택했다. 내연기관에 잔뼈가 굵은 노동자들을 도태시키고 전동화에 최적화된 노동력을 새로 뽑는 방식을 취하지 않았다. 츠비카우 공장의 9,500여 노동력, 수십여년간 내연기관차만 만들어 온 인력들을 전기차를 생산할 수 있는 인력으로 수년에 걸쳐 ‘트랜스폼’ 하는 방식을 택했다. 효율 대신 지속가능성을 앞세운 진짜 이유는 ‘사람’이었다.
츠비카우 공장의 교육을 담당했던 매티아스 로스는 한국의 취재진에게 ‘트랜스포메이션 체인지 프로그램’을 소개하면서 “2018년부터 2020년까지 3년에 걸쳐 320가지의 새로운 토픽을 제시하며 한 사람 한 사람을 설득하는 작업부터 시작했다”고 말했다.
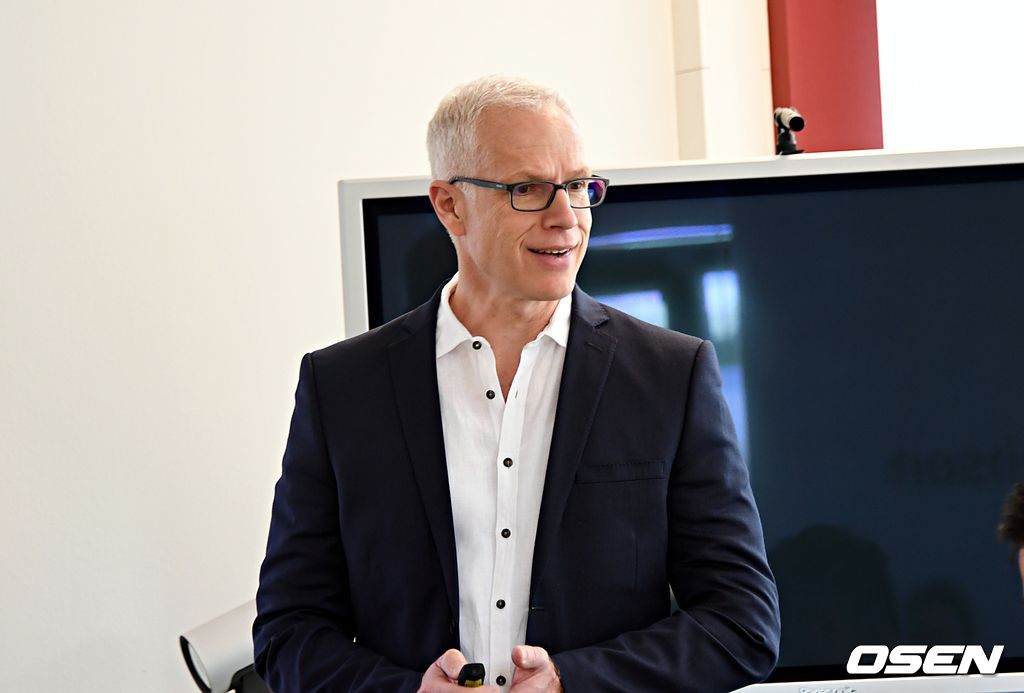
전기차를 생산하는 기술 교육부터 들이밀지 않았다. 폭스바겐그룹이라는 내연기관의 글로벌 강자가 왜 전동화로 대전환을 해야하는 지 설득하는 작업이 먼저였다. 묵직한 주제의 대화가 시작됐다. E 모빌리티, 디지털화, 커지고 있는 소프트웨어의 중요성 등 자동차를 둘러싼 글로벌 환경 변화를 보여주며 그들 스스로 답을 찾기를 기다렸다.
매티아스 로스는 “체인지 매니지먼트는 공장 설비만 바꾸는 작업이 아니었다. 더 중요한 건 사람들의 머리, 즉 의식을 바꿔 주는 일이었다. ‘전기’는 옳고 ‘내연기관’은 나쁘다는 식의 접근은 위험했다. 근로자들과 같은 눈높이에서 대화하며 ‘대전환’의 당위성을 스스로 깨닫도록 했다. 그 이후에 기술 교육이 이뤄졌다”고 말했다.
츠비카우 공장의 트랜스포메이션은 성공적이었다. 자연감소 인력을 제외한 인위적인 인력 감축은 없었고, 전환을 거부하며 낙오한 근로자 또한 한 명도 없었다. 회사도 같은 강도로 인내했다. 조립라인을 새로 깔고, 재교육을 실시하는 3년 동안 종전 임금 수준을 전액 보전했다.
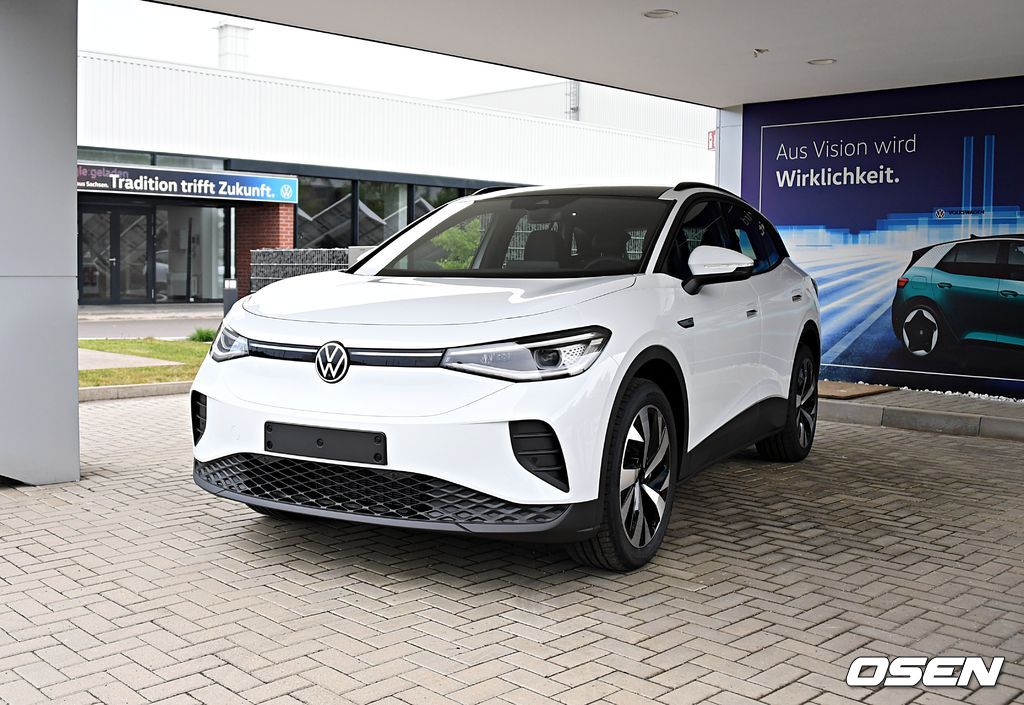
츠비카우 공장이 전기차 전용 생산공장으로 전환됨에 따라 공장의 파트너사들도 적극적으로 전동화에 나섰다. 츠비카우 공장 반경 15km 이내에 네 곳의 협력업체가 밀집한 산업단지가 있는데 현재까지 약 1억 3,000만 유로(약 1,744억 원)가 트렌스포메이션에 투자됐다. 탄소중립을 위한 폭스바겐그룹의 행동강령에 따라 공장의 협력업체들도 모두 100% 친환경 에너지를 사용해 전기차 부품을 생산하고 있다.
츠비카우의 사례는 폭스바겐그룹의 다른 공장을 트랜스포메이션 하는데 훌륭한 교과서로 활용될 것이다. 공장 설비를 재정비하면서 자동화 시스템도 높은 비중으로 들어왔다. 종전 공장의 자동화 비율이 85% 수준이었는데 전기차로 전환하면서 90% 수준으로 높아졌다. 안정을 찾은 츠비카우 공장은 내년에는 연간 30만대 생산을 목표로 하고 있다. 연간 30만대는 츠비카우 공장의 최대 케파다.
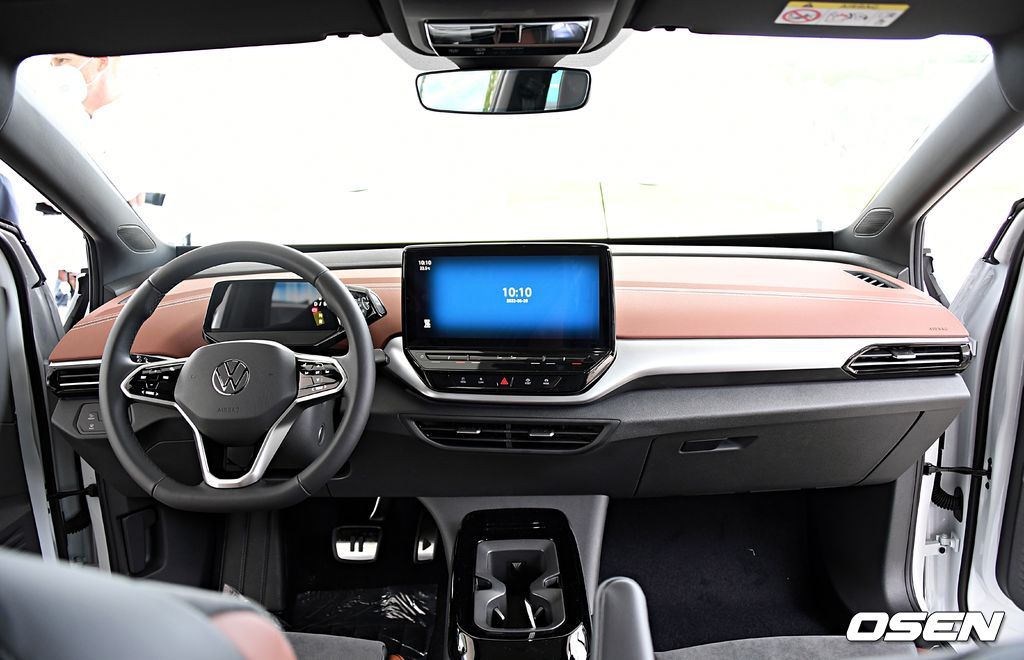
츠비카우 공장은 폭스바겐그룹의 모듈형 전동화 플랫폼 MEB((Modular Electric Drive Toolkit)를 기반으로 하는 6개 모델을 생산해 낸다. 폭스바겐 ID.3 와 ID.4 모델이 2020년 8월부터, 아우디 Q4 e-트론 모델이 2021년 3월부터 생산을 시작했다. 2022년 1월부터는 폭스바겐 ID.5도 이 곳에서 생산되고 있다. 아우디 Q4 스포트백 e-트론과 ID.3를 빼닮은 전기차 ‘쿠프라 본’도 생산을 시작했다.
츠비카우 공장에서 쏟아져 나오는 6종의 전기차 모델들은 폭스바겐그룹 ‘전기차 대전환’의 상징물이었다. 공장 사람들의 ‘대전환’ 과정을 직접 듣고서야 알아챘다. 85년 이상 내연기관차를 만들어 왔던 글로벌 브랜드의 전동화 과정은 결코 ‘금나와라 뚝딱!’이 아니었다. /100c@osen.co.kr